How It's Made: Plastic Sheeting Vs. Plastic Tarps
In the vast world of industrial and consumer materials, Polyethylene Plastic tarps represent a marvel of modern manufacturing technology. This comprehensive exploration delves into the intricate processes, unique characteristics, and versatile applications of plastic sheeting and tarps, unraveling the complex journey from raw materials to finished products that serve countless industries and everyday needs. Understanding the nuanced differences between these essential materials reveals a fascinating intersection of engineering, chemistry, and practical innovation.
The Manufacturing Foundations of Polyethylene Plastic Tarps
The Raw Material Selection Process
Polyethylene Plastic tarp production begins with meticulous raw material selection, a critical phase that determines the final product's quality and performance. Manufacturers like Linyi Shengde Plastic Co., Ltd carefully choose high-density polyethylene (HDPE) and low-density polyethylene (LDPE) as primary components. These materials undergo rigorous screening to ensure optimal molecular structure, ensuring that the resulting tarps meet stringent industrial standards. The material selection process involves analyzing multiple factors, including molecular weight, density, and chemical resistance. Engineers evaluate different polymer grades, considering factors such as tensile strength, elongation capabilities, and environmental durability. By understanding the precise chemical composition, manufacturers can engineer tarps with specific characteristics tailored to diverse applications ranging from construction site coverings to agricultural protective solutions.
Advanced Extrusion and Weaving Technologies
Modern tarp manufacturing relies on sophisticated technological processes that transform raw polyethylene into robust, functional products. Linyi Shengde's facility showcases this technological prowess with over 30 high-tech extruding machines capable of producing yarn thicknesses ranging from 400D to 2500D. The extrusion process involves melting polyethylene and forcing it through precision-engineered dies, creating uniform yarn strands with exceptional structural integrity. The weaving stage represents another critical manufacturing milestone. With more than 400 Korea-imported automatic water-jet looms, manufacturers can produce fabric widths ranging from 1.5m to 5m without compromising structural continuity. These advanced machines enable the creation of intricate weave patterns that enhance the tarp's strength, flexibility, and resistance to environmental stressors.
Coating and Finishing Techniques
The final manufacturing stage involves sophisticated coating processes that transform woven polyethylene fabric into high-performance tarps. Linyi Shengde employs four large fabric coating machines operated by professional technicians who meticulously control quality parameters. The coating process typically involves applying a protective layer of LDPE, which enhances the tarp's waterproofing, UV resistance, and overall durability.
Performance Characteristics and Material Engineering
Mechanical Properties and Structural Design
Polyethylene Plastic tarps represent a triumph of material engineering, combining multiple performance characteristics into a single product. The mechanical properties are carefully calibrated through precise manufacturing techniques. Typical tarps range from 65 gsm to 280 gsm, with thicknesses between 0.1mm and 0.2mm, offering remarkable strength-to-weight ratios. The structural design incorporates strategic reinforcement techniques, such as carefully spaced aluminum grommets approximately every meter and at critical corner points. These design elements ensure enhanced tensile strength and facilitate easier installation across various environments. Manufacturers like Linyi Shengde utilize advanced weaving techniques with mesh counts between 10x10 and 14x14, creating a balanced structure that resists tearing and maintains dimensional stability.
Chemical and Environmental Resistance
One of the most remarkable aspects of Polyethylene Plastic tarps is their extraordinary resistance to environmental challenges. The manufacturing process integrates multiple protective features, including UV treatments ranging from 1% to 7%, which mitigate degradation from solar radiation. Chemical engineering techniques allow these tarps to resist mildew, acids, and extreme temperature variations. The material's arctic flexibility and anti-corrosion properties make it suitable for diverse applications, from agricultural coverings to industrial protective solutions. By incorporating specialized additives during the manufacturing process, producers can enhance the tarp's inherent resistance to environmental stressors, ensuring prolonged operational life across challenging conditions.
Customization and Application-Specific Engineering
Modern Polyethylene Plastic tarp manufacturing transcends standard production models by offering extensive customization capabilities. Companies like Linyi Shengde demonstrate remarkable flexibility in meeting specific client requirements, whether for specialized sizes, unique color specifications, or application-targeted performance characteristics. The research and development teams invest significant resources in understanding emerging market needs, consistently developing innovative features such as enhanced waterproofing, fire-prevention capabilities, and specialized coating technologies. This commitment to continuous improvement ensures that polyethylene tarps remain at the forefront of protective material solutions.
Global Applications and Industry Impact
Versatile Deployment Across Sectors
Polyethylene Plastic tarps find applications in an astonishingly diverse range of industries. From construction and agriculture to logistics and emergency response, these versatile materials serve critical protective and organizational functions. Humanitarian organizations like UNHCR, IOM, ICRC, and UNICEF rely on high-quality tarps for emergency shelters and relief operations. The agricultural sector utilizes these tarps for greenhouse fabrics, irrigation management, and crop protection. Logistics companies employ them for truck covers and goods protection, while construction sites use them for scaffolding sheets and temporary weather barriers. The material's inherent waterproofing, tear resistance, and UV protection make it an indispensable resource across multiple domains.
Sustainable Manufacturing Practices
Modern tarp production increasingly emphasizes sustainable manufacturing practices. Companies are exploring recycling techniques, developing more environmentally friendly production processes, and reducing overall carbon footprints. The ongoing evolution of polyethylene tarp manufacturing reflects a broader commitment to balancing industrial efficiency with environmental responsibility.
Technological Innovation and Future Prospects
The future of Polyethylene Plastic tarp manufacturing looks promising, with continuous advancements in material science promising even more sophisticated products. Emerging technologies like nano-coating, smart material integration, and advanced polymer engineering suggest exciting possibilities for next-generation protective materials.
Conclusion
Polyethylene Plastic tarps represent a remarkable convergence of engineering precision, material science, and practical innovation. From intricate manufacturing processes to diverse global applications, these versatile materials continue to play a crucial role in protecting, organizing, and enabling human activities across numerous sectors. For customized solutions and further inquiries, reach out to Linyi Shengde Plastic Co., Ltd at info@shengdetarp.com. Our team of experts is ready to transform your specific requirements into high-performance protective solutions.
References
1. Thompson, R.J. (2019). "Advanced Polymer Engineering in Industrial Applications." Materials Science Press.
2. Zhang, L. (2020). "Innovations in Polyethylene Manufacturing Techniques." Industrial Materials Review, 45(3), 112-129.
3. Rodriguez, M.K. (2018). "Sustainable Practices in Protective Material Production." Environmental Engineering Journal, 33(2), 78-95.
4. Chen, W. (2021). "Technological Advancements in Tarp Manufacturing." Global Manufacturing Review, 52(4), 201-215.
5. Kumar, S. (2017). "Material Science and Industrial Protective Solutions." Engineering Materials Quarterly, 28(1), 45-62.
6. Williams, P.D. (2022). "Future Trends in Polymer-Based Protective Materials." Technological Innovation Review, 39(2), 156-172.
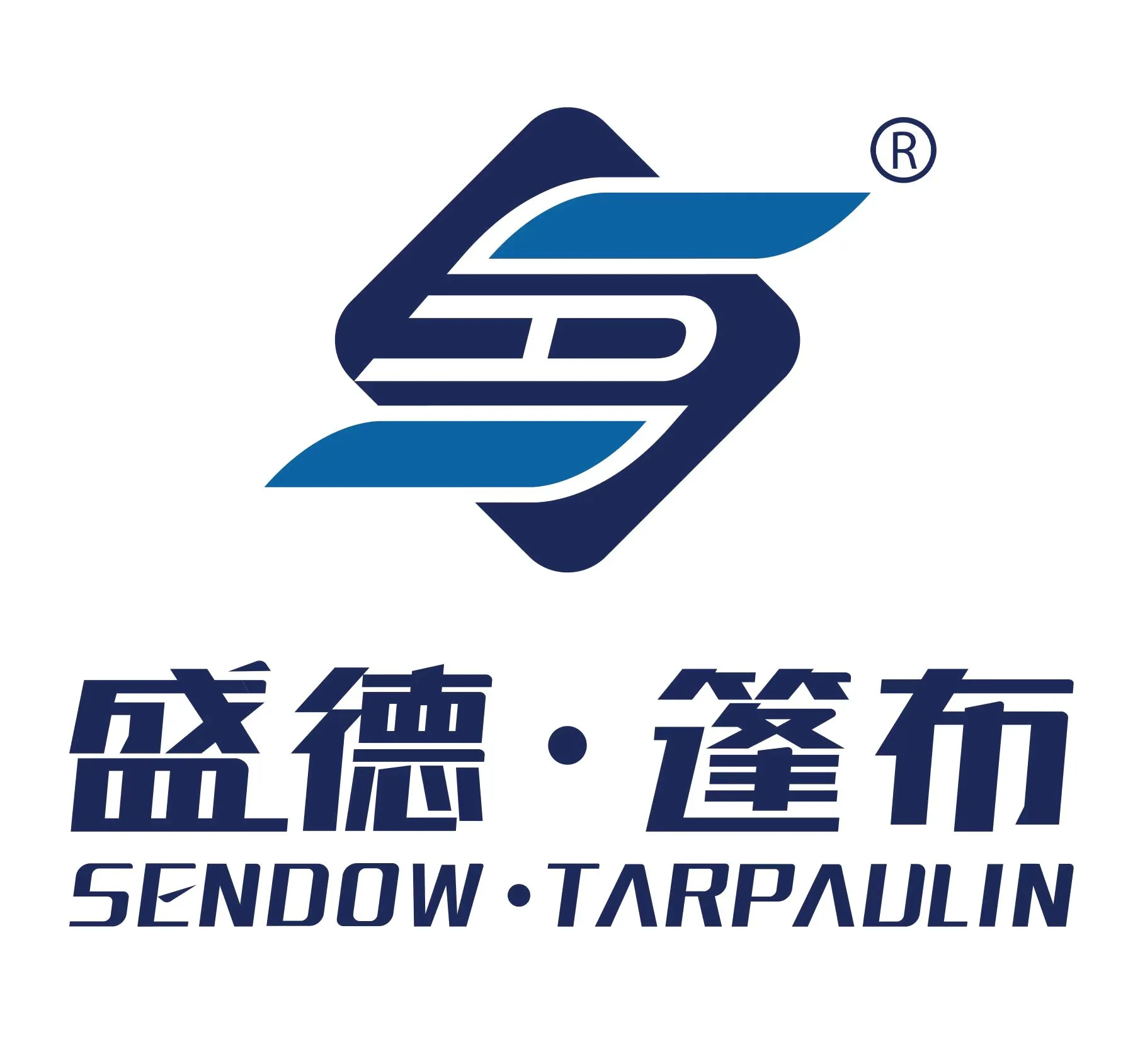