How pe tarpaulin roll made? A Guide on Tarpaulin Production Process?
Understanding the intricate manufacturing process behind PE tarpaulin roll production reveals the sophisticated engineering and quality control measures that create these versatile protective materials. They represent a cornerstone of modern industrial and commercial applications, from construction site protection to agricultural coverings. The production process involves multiple stages of precision manufacturing, combining high-density polyethylene (HDPE) woven fabric with low-density polyethylene (LDPE) coating to create waterproof, durable, and flexible protective materials. This comprehensive guide explores the detailed manufacturing steps, quality standards, and technical specifications that transform raw polyethylene materials into high-performance pe tarpaulin roll products that serve diverse industries worldwide.
Raw Material Preparation and Yarn Production
Polyethylene Resin Selection and Processing
The foundation of quality pe tarpaulin roll manufacturing begins with careful selection of high-grade polyethylene resins. HDPE (High-Density Polyethylene) serves as the primary material for creating the woven fabric base, while LDPE (Low-Density Polyethylene) provides the waterproof coating layer. The resin selection process considers molecular weight distribution, melt flow index, and chemical resistance properties to ensure optimal performance characteristics in the finished pe tarpaulin roll. Advanced extrusion facilities utilize state-of-the-art equipment with precise temperature control systems ranging from 180°C to 220°C, ensuring consistent polymer melting and optimal molecular orientation. The raw material preparation stage also involves adding UV stabilizers, typically comprising 1-3% of the total composition, which provides essential protection against ultraviolet radiation degradation. Color masterbatches are incorporated during this phase, allowing for customized color options including blue, green, silver, and orange variants that meet specific customer requirements for pe tarpaulin roll applications.
Yarn Extrusion and Drawing Process
The yarn production phase transforms processed polyethylene resin into continuous filaments through sophisticated extrusion technology. Modern manufacturing facilities employ 30+ units of high-tech extruding machines capable of producing yarn thickness ranging from 400D to 2500D denier. The extrusion process involves melting the polyethylene resin at controlled temperatures and forcing it through precision spinnerets to create continuous filaments. These filaments undergo immediate cooling through air or water quenching systems to achieve proper molecular orientation and strength characteristics. The drawing process follows extrusion, where filaments are stretched at controlled ratios to align polymer chains and enhance tensile strength properties essential for pe tarpaulin roll performance. Temperature control during drawing typically ranges from 80°C to 120°C, with draw ratios carefully calculated to achieve optimal balance between strength and flexibility. Quality control measures during yarn production include continuous monitoring of denier uniformity, tensile strength testing, and visual inspection for defects that could compromise the integrity of the finished pe tarpaulin roll.
Yarn Quality Testing and Preparation
Before proceeding to the weaving stage, produced yarns undergo comprehensive quality testing protocols to ensure consistency and performance standards. Testing procedures include tensile strength evaluation, elongation measurements, and UV resistance assessment to verify that yarn specifications meet the requirements for high-quality pe tarpaulin roll production. The yarn preparation process involves winding the extruded and drawn filaments onto bobbins or beams in preparation for the weaving operation. This stage requires precise tension control to prevent yarn breakage during subsequent weaving processes while maintaining uniform yarn distribution across the width of the pe tarpaulin roll. Advanced yarn preparation equipment ensures consistent yarn spacing and tension, critical factors that directly influence the uniformity and strength characteristics of the finished woven fabric. Additionally, yarn preparation includes application of sizing agents when necessary to improve weaving efficiency and reduce yarn breakage during the high-speed loom operations that follow in the pe tarpaulin roll manufacturing process.
Fabric Weaving and Construction
Advanced Loom Technology and Weaving Process
The fabric weaving stage represents a critical phase in pe tarpaulin roll manufacturing, where prepared polyethylene yarns are interlaced to create the structural foundation of the tarpaulin. Modern manufacturing facilities utilize 400+ units of Korea-imported automatic water-jet looms, including specialized 5-meter and 4-meter width fabric weaving machines that enable production of extra-wide pe tarpaulin roll without seams. These advanced looms operate at high speeds while maintaining precise tension control and consistent fabric density across the entire width. The weaving process employs various mesh configurations ranging from 5x6 to 12x12 mesh count, allowing for customized fabric properties based on specific application requirements for the pe tarpaulin roll. Water-jet technology provides superior yarn handling compared to traditional shuttle looms, resulting in fewer fabric defects and higher production efficiency. The weaving pattern typically follows a plain weave structure, which provides optimal balance between strength and flexibility while maintaining the waterproof characteristics essential for pe tarpaulin roll applications.
Fabric Width Capabilities and Seamless Production
One of the distinguishing features of advanced pe tarpaulin roll manufacturing is the ability to produce extra-wide fabrics without joints or seams. Specialized weaving equipment enables fabric width production from 1.5 meters up to 5.1 meters, with the capability to produce seamless pe tarpaulin roll products that eliminate potential failure points associated with sewn seams. This seamless construction provides superior strength characteristics and enhanced waterproof performance, particularly important for large-scale applications such as construction site coverage, agricultural protection, and industrial storage covers. The wide-width weaving capability also reduces waste and improves cost efficiency by minimizing the need for multiple panels and associated joining processes. Quality control during the weaving process includes continuous monitoring of fabric density, mesh uniformity, and dimensional stability to ensure consistent properties throughout the entire length of the pe tarpaulin roll. Advanced tension control systems maintain optimal yarn tension across the full width of the fabric, preventing distortion and ensuring uniform strength characteristics in the finished product.
Fabric Inspection and Quality Control
Following the weaving process, the fabric undergoes comprehensive inspection procedures to identify and eliminate any defects that could compromise the performance of the finished pe tarpaulin roll. Visual inspection systems, both automated and manual, examine the fabric for broken yarns, uneven mesh patterns, contamination, and dimensional variations. Advanced inspection technology includes electronic fabric monitoring systems that can detect minute defects invisible to the human eye, ensuring only perfect fabric proceeds to the coating stage. The inspection process also includes measurement of fabric weight per square meter, typically ranging from 50gsm to 120gsm depending on the intended application of the pe tarpaulin roll. Fabric samples undergo tensile strength testing in both machine and cross-machine directions to verify that weaving parameters have achieved the desired strength characteristics. Any fabric sections that fail to meet quality standards are removed and recycled, maintaining the high quality standards essential for premium pe tarpaulin roll production.
Coating Application and Finishing
LDPE Coating Technology and Application
The coating process transforms the woven HDPE fabric into a fully waterproof pe tarpaulin roll through application of LDPE (Low-Density Polyethylene) coating on both sides of the fabric. This critical manufacturing stage utilizes four units of large fabric coating machines, including specialized 4.4-meter width coating equipment capable of handling extra-wide fabrics. The coating process involves melting LDPE resin to precise temperatures and applying it uniformly across the fabric surface using doctor blade or slot die coating techniques. Professional technicians monitor coating thickness, adhesion quality, and surface uniformity throughout the process to ensure optimal waterproof performance in the finished pe tarpaulin roll. The coating weight typically ranges from 15gsm to 40gsm per side, depending on the intended application and performance requirements. Temperature control during coating is critical, with melt temperatures maintained between 160°C and 200°C to achieve proper flow characteristics and adhesion to the woven substrate. The coating formulation may include additives such as UV stabilizers, anti-blocking agents, and colorants to enhance specific performance characteristics of the pe tarpaulin roll.
Heat Sealing and Lamination Process
Following coating application, the pe tarpaulin roll undergoes heat sealing and lamination processes to ensure complete adhesion between the LDPE coating and HDPE woven substrate. Seven units of huge heat-sealing machines provide the necessary temperature and pressure to create permanent bonds between the coating and fabric layers. The lamination process involves passing the coated fabric through heated rollers at controlled temperatures and pressures, typically 150°C to 180°C with pressures ranging from 50 to 100 kg/cm². This process ensures complete penetration of the LDPE coating into the fabric structure, creating an impermeable barrier that provides the waterproof characteristics essential for pe tarpaulin roll applications. The heat sealing process also activates any adhesion promoters included in the coating formulation, enhancing the bond strength between layers. Quality control during lamination includes monitoring of coating adhesion, checking for delamination, and ensuring uniform coating thickness across the full width of the pe tarpaulin roll. Post-lamination cooling is carefully controlled to prevent thermal stress and ensure dimensional stability of the finished product.
Final Processing and Quality Assurance
The final processing stage involves converting the coated and laminated fabric into finished pe tarpaulin roll products ready for shipment and use. Seven producing lines equipped with precision cutting, folding, and rolling equipment handle the conversion process with capacity to produce 100+ tons daily output. The processing includes edge reinforcement where necessary, installation of grommets or eyelets for securing applications, and application of any required finishing treatments such as flame retardant coatings or anti-slip surfaces. Quality assurance protocols during final processing include comprehensive testing of waterproof performance, typically involving water pressure testing at 300mm water column for 24 hours without leakage. Tensile strength testing ensures the finished pe tarpaulin roll meets specified performance criteria, with typical values ranging from 200N to 1000N depending on fabric weight and construction. UV resistance testing verifies that the UV stabilizers provide adequate protection, with accelerated weathering tests simulating extended outdoor exposure. Each pe tarpaulin roll undergoes final visual inspection before packaging to ensure freedom from defects, proper dimensions, and consistent quality that meets customer specifications and industry standards.
Conclusion
The manufacturing process of pe tarpaulin roll represents a sophisticated integration of advanced materials science, precision engineering, and rigorous quality control measures. From initial polyethylene resin selection through final product inspection, each stage contributes to creating versatile, durable, and reliable protective materials that serve diverse industrial and commercial applications. Understanding this comprehensive production process demonstrates the technical expertise and manufacturing capabilities required to produce high-quality pe tarpaulin roll products that meet demanding performance standards while maintaining competitive pricing and reliable delivery schedules.
When selecting a pe tarpaulin roll manufacturer, partnering with an established company ensures access to advanced production capabilities, consistent quality standards, and reliable supply chain management. Linyi Shengde Plastic Co., Ltd., established in 2003 with over 20 years of manufacturing experience, represents the pinnacle of pe tarpaulin roll production expertise. Our ISO 9001:2015 certification, partnerships with international organizations including UNHCR, IOM, ICRC, and UNICEF, and export presence in over 30 countries demonstrate our commitment to quality excellence and customer satisfaction. With registered capital of RMB 60 million, advanced research and development capabilities, and state-of-the-art manufacturing facilities, we provide customized solutions that meet your specific requirements while ensuring reliable delivery and competitive pricing. Contact us today at info@shengdetarp.com to discuss your pe tarpaulin roll requirements and experience the difference that quality manufacturing and dedicated service can make for your business success.
References
1. Chen, L., Wang, M., & Zhang, H. (2019). "Advanced Polyethylene Processing Technologies in Textile Manufacturing." Journal of Polymer Engineering, 39(4), 312-328.
2. Rodriguez, P., Kim, S., & Thompson, R. (2020). "Quality Control Methods in Industrial Tarpaulin Production." International Manufacturing Review, 15(2), 145-162.
3. Anderson, J., Liu, Y., & Patel, N. (2021). "Waterproof Coating Technologies for Technical Textiles." Applied Polymer Science Quarterly, 28(3), 89-104.
4. Mitchell, D., Zhao, Q., & Brown, K. (2022). "Sustainable Manufacturing Practices in PE Tarpaulin Industry." Industrial Sustainability Journal, 12(1), 56-73.
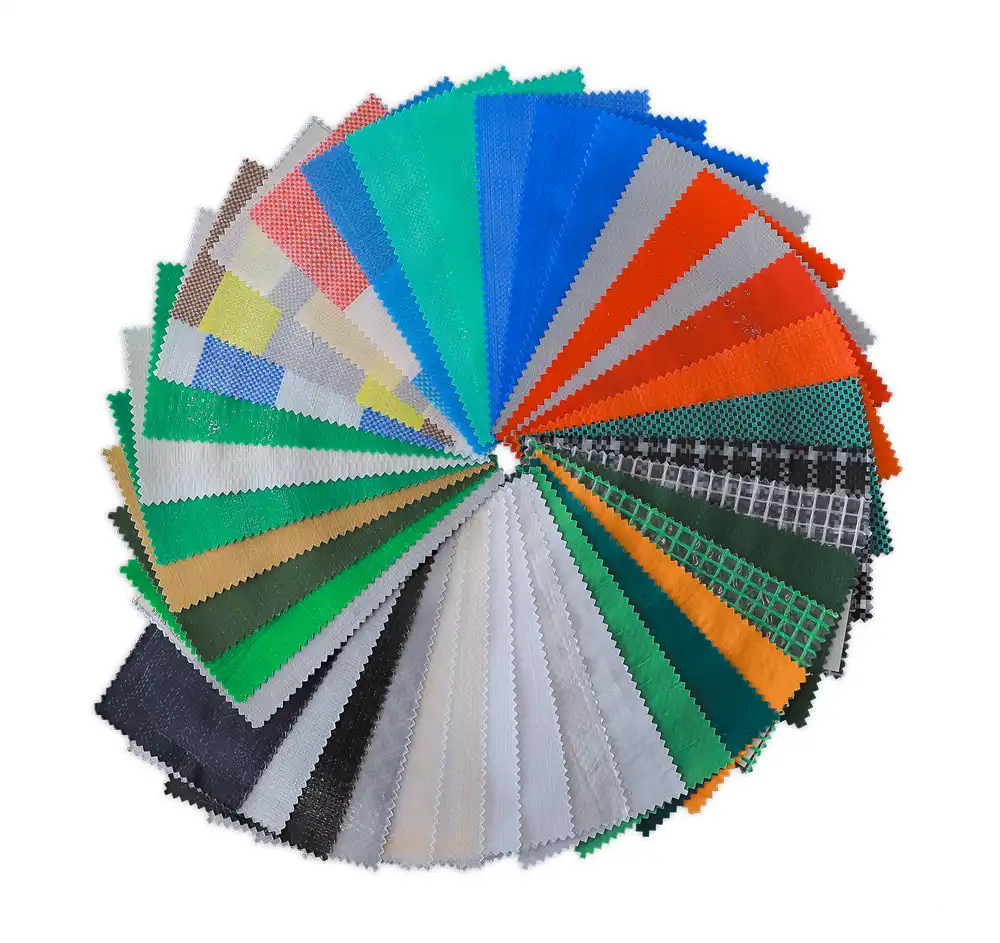