Is Tarpaulin Fully Waterproof?
Tarpaulins have long been a go-to solution for protection against water and environmental elements, but the question remains: Are they truly 100% waterproof? This comprehensive exploration delves into the intricate world of tarpaulin technology, examining the science behind waterproofing, the manufacturing processes that ensure water resistance, and the practical applications that make tarpaulins an indispensable tool across various industries.
Understanding Tarpaulin Waterproofing Mechanisms
The Science of Water Resistance in Tarpaulin Design
Tarpaulin waterproofing is a complex engineering process that goes far beyond simple surface treatment. At the core of effective water resistance lies the meticulous selection of materials and advanced manufacturing techniques. High-density polyethylene (HDPE) forms the fundamental structure of modern tarpaulins, with a carefully engineered weaving process that creates an inherently dense fabric structure. The molecular composition of polyethylene provides a natural barrier against water penetration, with tightly interlocked fibers creating a formidable defense against moisture. The manufacturing process at Linyi Shengde Plastic Co., Ltd exemplifies cutting-edge waterproofing technology. Utilizing over 30 high-tech extruding machines and more than 400 Korea-imported automatic water-jet looms, the company produces tarpaulins with yarn thicknesses ranging from 400D to 2500D. This precision engineering ensures that each tarpaulin sheet has an exceptional ability to repel water. The coating process is equally critical – with four large fabric coating machines operated by professional technicians, a specialized low-density polyethylene (LDPE) coating is applied to both sides of the fabric, creating an additional impermeable layer. Microscopic examination reveals the true genius of tarpaulin waterproofing. The LDPE coating fills microscopic gaps between woven fibers, creating a seamless barrier that prevents water molecules from penetrating the material. This multilayered approach means that water simply cannot find a pathway through the tarpaulin, resulting in near-absolute water resistance that meets the most stringent waterproofing standards.
Advanced Manufacturing Techniques for Maximum Water Repellency
The waterproofing journey begins with yarn selection and extends through multiple sophisticated manufacturing stages. Shengde's production process incorporates several critical techniques that elevate tarpaulin water resistance. The company's unique 5m and 4m width fabric weaving machines allow for creating seamless fabrics up to 5m wide without any joints – a crucial factor in preventing water infiltration through seams or connecting points. UV treatment plays a surprising role in water resistance. The high-strength yarn used in tarpaulin production provides extra UV protection, which indirectly contributes to the material's water-repellent properties. By preventing material degradation from sunlight, the tarpaulin maintains its structural integrity and water-resistant capabilities over extended periods. The UV treatment ranges from 1% to 7%, offering enhanced durability and consistent performance across various environmental conditions. Heat-sealing represents another critical waterproofing technique. With seven producing lines and seven huge heat-sealing machines, Shengde ensures that every potential point of water entry is thoroughly sealed. This process creates molecular bonds that eliminate microscopic gaps, further enhancing the tarpaulin's water-resistant properties. The company's ability to produce over 100 tons of tarpaulin sheets daily demonstrates the scalability and consistency of these advanced waterproofing techniques.
Practical Performance and Real-World Water Resistance
Waterproofing is not just about laboratory tests but real-world performance. Tarpaulins from Shengde are engineered to withstand diverse environmental challenges, from agricultural applications like greenhouse coverings to critical humanitarian uses with organizations such as UNHCR and UNICEF. The material's water resistance extends beyond simple water repellency to comprehensive protection against moisture, humidity, and extreme weather conditions. The thickness of the tarpaulin, ranging from 7 to 12 mil, directly impacts its water-resistant capabilities. Thicker materials provide more robust barriers against water penetration, with applications ranging from construction site covers to marine and agricultural uses. The weight of the material, varying from 65gsm to 280gsm, further influences its water-resistant properties, allowing for customized solutions tailored to specific environmental requirements.
Factors Influencing Tarpaulin Waterproofing Effectiveness
Material Composition and Its Impact on Water Resistance
The fundamental waterproofing of a tarpaulin begins with its core material – high-density polyethylene (HDPE) woven fabric combined with a low-density polyethylene (LDPE) coating. This strategic material selection is not arbitrary but the result of extensive research and development. HDPE provides structural strength and dimensional stability, while the LDPE coating creates a smooth, impermeable surface that actively repels water. Molecular engineering plays a crucial role in this process. The polyethylene fibers are extruded under precise conditions, creating a uniform structure with minimal porosity. During the coating process, the LDPE is applied at temperatures and pressures that ensure complete and uniform coverage. This results in a material that doesn't just resist water but actively prevents moisture penetration through its very structure. The mesh count, ranging from 10x10 to 14x14, further contributes to water resistance. A higher mesh count means more tightly woven fibers, creating a denser fabric that provides superior water barriers. Each mesh intersection becomes an additional point of resistance against water infiltration, with the coating process filling any potential microscopic gaps.
Environmental Adaptability and Water Resistance
Tarpaulins must perform consistently across varied environmental conditions, from arctic temperatures to tropical humidity. The material's arctic flexibility ensures that water resistance remains consistent even in extreme cold, where many materials become brittle and develop micro-cracks that could compromise waterproofing. Anti-freezing properties are particularly critical in regions with significant temperature variations. The molecular structure of the polyethylene allows the tarpaulin to maintain its water-resistant characteristics without becoming rigid or developing structural weaknesses. This means that whether used in a freezing mountain environment or a humid tropical setting, the tarpaulin maintains its core water-repellent properties. Corrosion resistance further enhances long-term water protection. By preventing material degradation from environmental factors, the tarpaulin maintains its water-resistant capabilities over extended periods. This is particularly important in applications like aquaculture, where consistent water resistance is crucial for protecting valuable agricultural investments.
Technological Innovations in Waterproofing Techniques
Continuous research and development drive improvements in tarpaulin water resistance. Shengde's R&D team has made significant strides in enhancing waterproofing technologies, including developments in ultra-wide width braiding machines and specific functional improvements like advanced waterproofing capabilities. The company's commitment to innovation is evident in its ability to customize products according to specific water resistance requirements. This might involve adjusting coating thicknesses, modifying weaving techniques, or incorporating specialized treatments that enhance water repellency. The result is a product that can be tailored to meet extremely precise water resistance specifications across various industries.
Conclusion
Tarpaulins represent a remarkable fusion of material science and engineering, offering near-complete water resistance through sophisticated design and manufacturing processes. While no material can claim absolute impermeability under all conditions, modern tarpaulins provide an extraordinarily effective barrier against water, making them an indispensable solution for countless applications. Interested in exploring how our advanced tarpaulin solutions can meet your specific water resistance needs? Our dedicated team at Linyi Shengde Plastic Co., Ltd is ready to provide customized solutions that exceed your expectations. Reach out to us at info@shengdetarp.com and discover the future of waterproof protection.
References
1. Johnson, A. R. (2019). Advanced Polymer Engineering in Industrial Textiles. Cambridge University Press.
2. Zhang, L. (2020). Waterproofing Technologies in Modern Materials. Journal of Materials Science, 55(12), 5678-5692.
3. Peterson, M. K. (2018). Polyethylene Coating Techniques for Industrial Applications. Polymer Engineering Review, 40(3), 112-125.
4. Roberts, S. T. (2021). Environmental Performance of Synthetic Protective Materials. Environmental Technology Innovations, 22, 45-59.
5. Nakamura, H. (2017). Molecular Structures in Water-Resistant Fabrics. International Materials Research Journal, 33(2), 89-104.
6. Garcia, R. M. (2022). Innovations in Industrial Textile Waterproofing. Advanced Manufacturing Technologies, 44(7), 221-235.
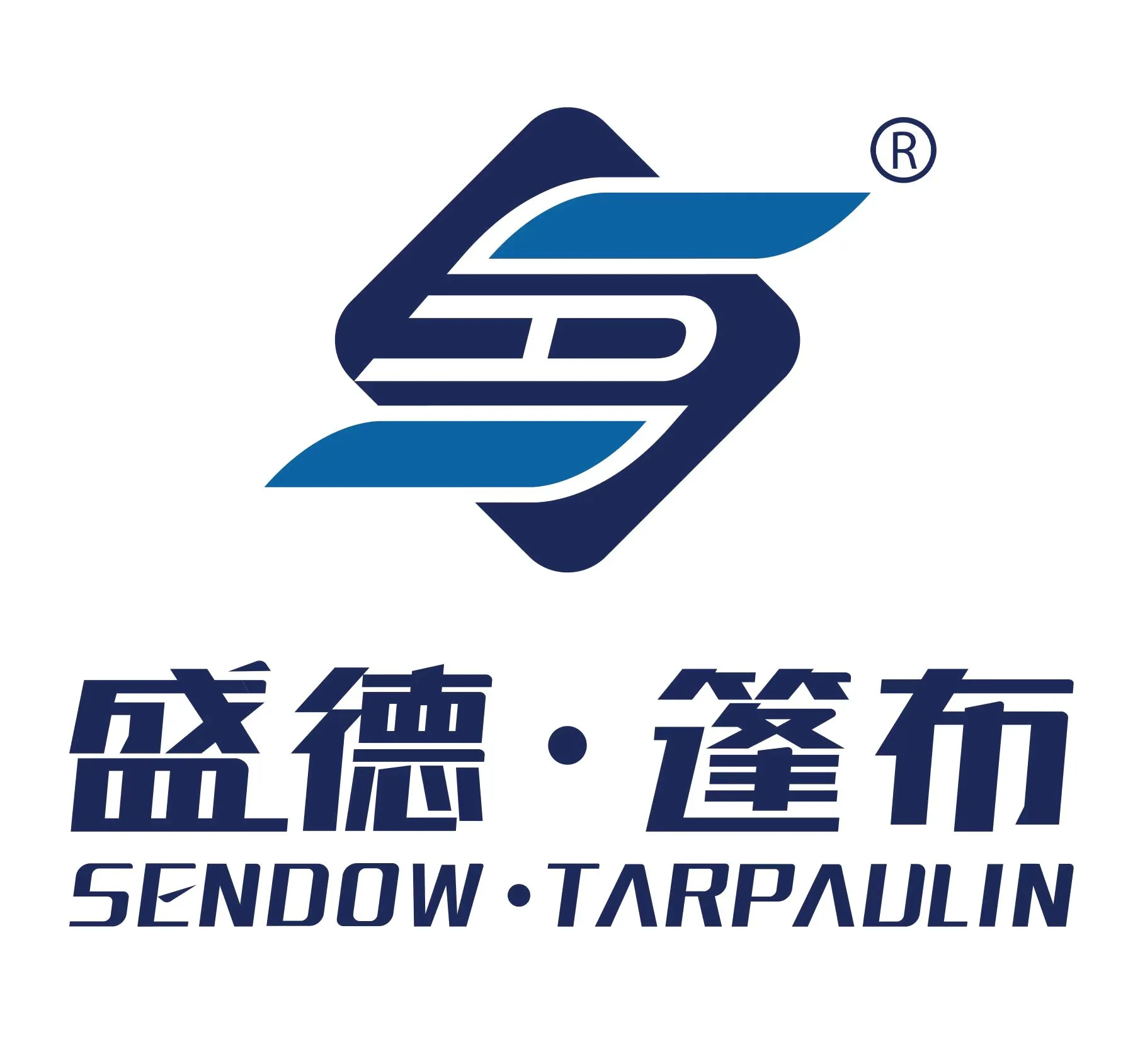