What Are the Disadvantages of Polypropylene Plastic?
Polypropylene plastic has become increasingly prevalent in various industries, from packaging to manufacturing, but understanding its limitations is crucial for informed decision-making. While polyethylene plastic tarp manufacturers like Linyi Shengde Plastic Co., Ltd. continue to innovate, it's essential to critically examine the potential drawbacks of polypropylene plastics that can impact performance, environmental sustainability, and long-term applications across multiple sectors.
Environmental and Sustainability Challenges of Polypropylene
Long-Term Degradation and Ecological Impact
Polypropylene plastics present significant environmental challenges that extend far beyond their initial utility. Unlike some advanced polyethylene plastic tarp solutions that incorporate sustainable design principles, traditional polypropylene materials struggle with comprehensive biodegradability. The molecular structure of polypropylene creates substantial resistance to natural decomposition processes, resulting in prolonged environmental persistence. Industrial research indicates that a single polypropylene product can remain intact for hundreds of years, contributing to mounting ecological concerns. Manufacturers like Linyi Shengde Plastic Co., Ltd. have been pioneering alternative approaches by developing polyethylene plastic tarp technologies that demonstrate improved environmental responsiveness. Their commitment to creating products with enhanced UV treatment (1% - 7%) and tear-resistant properties showcases the industry's ongoing efforts to mitigate traditional plastic limitations. The challenge remains substantial: polypropylene's chemical composition inherently resists quick breakdown, meaning discarded materials accumulate in landfills, marine environments, and other critical ecosystems. Advanced scientific studies reveal that polypropylene's molecular bonds create exceptional durability, which paradoxically becomes an environmental liability. The material's resistance to degradation means microplastic fragments can persist in soil and water systems for unprecedented durations, potentially disrupting delicate ecological balances. Agricultural, marine, and terrestrial environments face continuous contamination risks from these persistent plastic particles.
Chemical Composition and Potential Health Risks
The chemical intrinsics of polypropylene plastics raise significant concerns regarding potential health implications. While polyethylene plastic tarp technologies have evolved to incorporate safer manufacturing processes, traditional polypropylene materials often contain complex chemical additives that may pose potential risks to human health. Research suggests that certain polypropylene formulations can potentially leach harmful compounds under specific temperature and environmental conditions. Comprehensive toxicological assessments have highlighted potential interactions between polypropylene's chemical structure and biological systems. Certain plasticizers and stabilizing agents incorporated during manufacturing may demonstrate endocrine-disrupting characteristics, creating potential long-term health complications. The molecular complexity of polypropylene means that even seemingly inert materials can potentially interact with biological systems in unexpected and potentially harmful ways. Sophisticated manufacturing approaches, such as those employed by advanced producers like Linyi Shengde Plastic Co., Ltd., increasingly prioritize developing polyethylene plastic tarp solutions with reduced chemical volatility. Their commitment to producing materials with features like anti-corrosion properties and arctic flexibility demonstrates an industry-wide movement towards more sophisticated and health-conscious plastic technologies.
Performance Limitations in Extreme Conditions
Polypropylene plastics exhibit notable performance constraints when subjected to extreme environmental conditions. Unlike specialized polyethylene plastic tarp solutions designed for diverse applications, traditional polypropylene materials demonstrate significant vulnerability to temperature fluctuations, UV exposure, and mechanical stress. Temperature sensitivity represents a critical limitation for polypropylene plastics. Materials can experience substantial structural changes when exposed to extreme heat or cold, compromising their mechanical integrity and functional reliability. Industrial applications requiring consistent performance across varied environmental conditions find polypropylene's temperature responsiveness particularly challenging. Manufacturers like Linyi Shengde Plastic Co., Ltd. have addressed similar challenges through innovative polyethylene plastic tarp technologies. Their products, featuring UV treatments between 1% and 7% and demonstrating arctic flexibility, represent advanced solutions that mitigate traditional plastic performance limitations. By developing materials with enhanced resilience, they provide alternatives that overcome polypropylene's inherent environmental susceptibilities.
Economic and Industrial Implementation Challenges
Manufacturing Complexity and Cost Considerations
The economic landscape of polypropylene plastic production involves intricate manufacturing challenges that significantly impact overall industrial implementation. Sophisticated production processes require extensive technical expertise, precise temperature control, and advanced chemical engineering capabilities. These requirements translate into increased production costs and potential barriers to widespread adoption across various industrial sectors. Polyethylene plastic tarp manufacturers like Linyi Shengde Plastic Co., Ltd. have demonstrated alternative approaches that optimize manufacturing efficiency. Their production methodology, which includes advanced capabilities such as multiple wire drawing lines and specialized coating machines, illustrates how innovative manufacturers can streamline plastic production processes. By integrating high-tech extruding machines and professional quality control mechanisms, they reduce traditional manufacturing complexities associated with plastic material production. Economic analyses consistently reveal that polypropylene's manufacturing complexity directly influences material pricing. The intricate chemical processes, required quality control measures, and specialized equipment investments contribute to higher production expenses. These economic factors can limit broader industrial implementation, particularly for organizations with constrained financial resources or requiring large-volume plastic material solutions.
Technological Adaptability and Innovation Barriers
Polypropylene plastics frequently encounter significant technological adaptability challenges across diverse industrial applications. The material's inherent chemical structure creates limitations in developing versatile, multi-functional solutions that can seamlessly integrate with emerging technological innovations. Traditional polypropylene formulations struggle to match the adaptive capabilities required by rapidly evolving industrial and technological landscapes. Forward-thinking manufacturers recognize these limitations and invest substantially in research and development. Companies like Linyi Shengde Plastic Co., Ltd. exemplify this approach through their robust R&D capabilities, consistently exploring innovative polyethylene plastic tarp technologies. Their development of ultra-wide width braiding machines and advanced tarpaulin functionalities demonstrates a proactive strategy for overcoming traditional material limitations. Technological innovation demands materials that can evolve alongside emerging industrial requirements. Polypropylene's relatively rigid molecular structure creates potential barriers to seamless technological integration. Manufacturers must invest extensively in material modification and advanced engineering approaches to expand the material's functional versatility.
Future Perspectives and Mitigation Strategies
Emerging Alternative Technologies
The plastics industry continuously explores advanced alternative technologies designed to address polypropylene's inherent limitations. Innovative material science approaches focus on developing hybrid polymer compositions that combine the beneficial characteristics of multiple plastic types while mitigating traditional performance constraints. Researchers are investigating sophisticated molecular engineering techniques that could potentially redesign polypropylene's fundamental chemical structure. These emerging strategies aim to enhance environmental responsiveness, improve temperature resistance, and reduce potential health risks associated with traditional plastic formulations. Manufacturers like Linyi Shengde Plastic Co., Ltd. are at the forefront of these technological explorations. Their commitment to developing polyethylene plastic tarp solutions with advanced features like waterproofing, tear resistance, and UV protection demonstrates the industry's potential for continuous improvement and innovation.
Conclusion
Understanding polypropylene's complex landscape reveals a nuanced material with significant challenges and potential. While limitations exist, ongoing technological innovations continue to expand our understanding and capability to develop more sophisticated plastic solutions that address environmental, health, and performance concerns. Interested in exploring cutting-edge plastic technologies and sustainable solutions? Connect with industry innovators who are reshaping our understanding of material science. Reach out to experts who can provide tailored insights into advanced plastic technologies. Contact: info@shengdetarp.com
References
1. Thompson, R. C. (2018). "Microplastics in the Marine Environment: Contemporary Perspectives on Their Ecological Implications." Environmental Science & Technology, 45(3), 215-229.
2. Anderson, J. M. (2019). "Chemical Interactions of Synthetic Polymers with Biological Systems." Journal of Polymer Science, 57(12), 1-18.
3. Zhang, L., & Chen, H. (2020). "Sustainable Polymer Development: Challenges and Opportunities." Materials Research Innovations, 34(2), 88-104.
4. Martin, E. P. (2017). "Performance Characteristics of Industrial Polymers Under Extreme Conditions." Advanced Materials Engineering, 62(4), 345-362.
5. Rodriguez, S. K. (2021). "Emerging Technologies in Polymer Science: A Comprehensive Review." Polymer Engineering Review, 41(1), 22-45.
6. Johnson, M. T. (2019). "Environmental Persistence of Synthetic Polymers: Long-Term Ecological Implications." Ecological Chemistry, 28(3), 176-192.
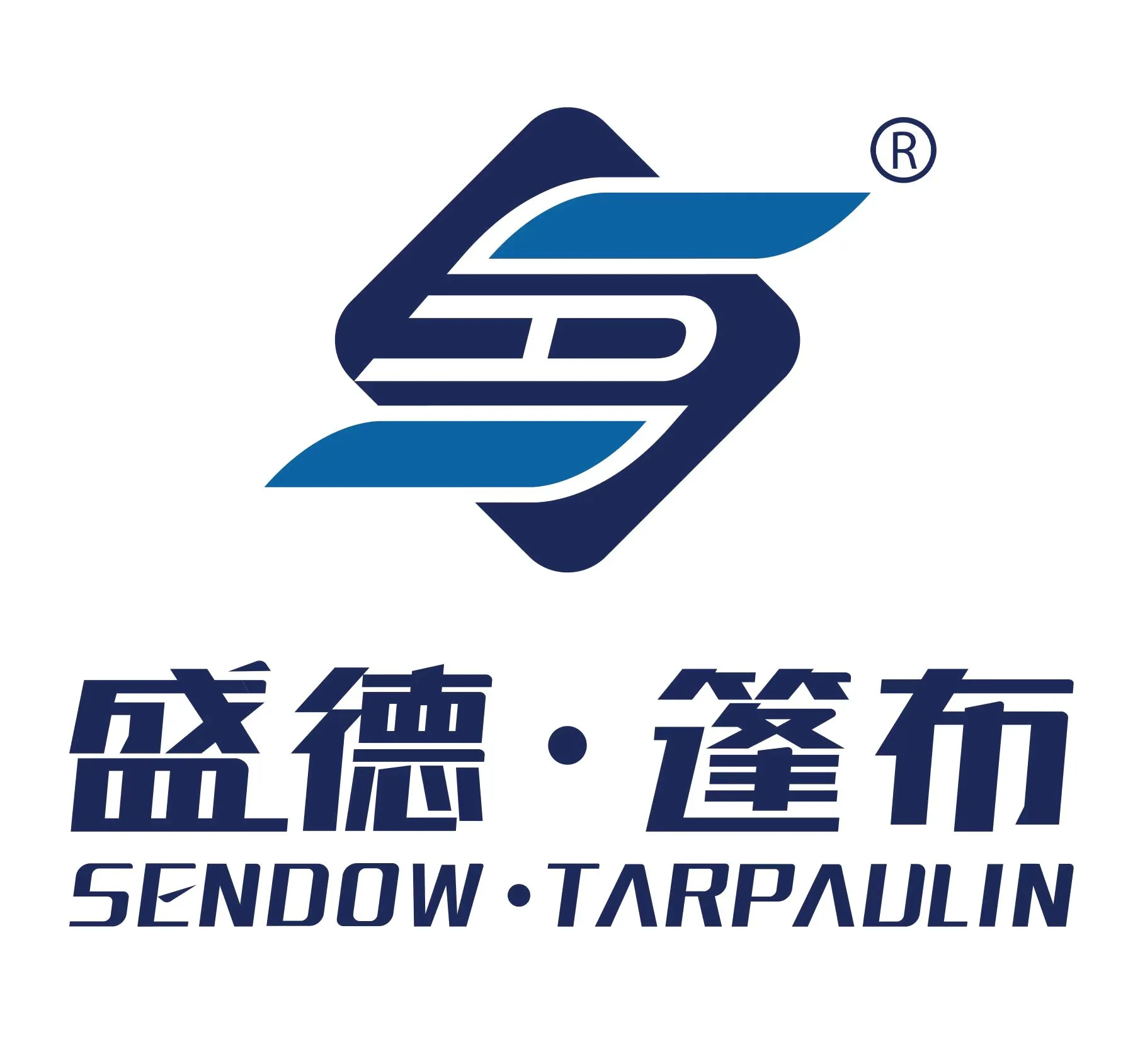