What Is Polyethylene Fabric? | PE vs. HDPE Fabric Materials?
Polyethylene fabric represents one of the most versatile and widely utilized synthetic materials in modern industrial applications, offering exceptional durability, chemical resistance, and cost-effectiveness across numerous sectors. As manufacturers and procurement specialists increasingly seek reliable fabric solutions for diverse applications ranging from agricultural coverings to industrial packaging, understanding the fundamental properties and distinctions between different polyethylene variants becomes crucial for informed decision-making. PE fabric, derived from polyethylene polymers, provides outstanding performance characteristics that make it indispensable in construction, agriculture, marine, and emergency response industries. The comparison between standard polyethylene and high-density polyethylene (HDPE) materials reveals significant differences in molecular structure, mechanical properties, and application suitability that directly impact product selection and performance outcomes.
Understanding Polyethylene Fabric Composition and Manufacturing
Chemical Structure and Polymer Characteristics
Polyethylene fabric emerges from the polymerization of ethylene monomers, creating long-chain hydrocarbon polymers that exhibit remarkable stability and resistance to environmental degradation. The manufacturing process involves sophisticated extrusion techniques where polyethylene pellets undergo heating and compression to form continuous filaments that are subsequently woven into fabric structures. It demonstrates exceptional chemical inertness, making it highly resistant to acids, bases, alcohols, and most organic solvents, which explains its widespread adoption in chemical processing and storage applications. The molecular weight distribution within polyethylene chains directly influences the fabric's mechanical properties, with higher molecular weight variants offering superior tensile strength and tear resistance. Modern manufacturing techniques allow for precise control of polymer density, crystallinity, and molecular orientation, enabling producers to tailor PE fabric characteristics to specific application requirements while maintaining consistent quality standards throughout production cycles.
Production Methods and Quality Control
The transformation of raw polyethylene into high-performance fabric involves multiple sophisticated processing stages, beginning with polymer preparation and extending through extrusion, weaving, and finishing operations. Contemporary PE fabric production utilizes advanced water-jet looms and computerized control systems to ensure uniform thread tension, consistent weave patterns, and optimal fabric density characteristics. Quality control measures encompass comprehensive testing protocols that evaluate tensile strength, tear resistance, UV stability, and dimensional stability under various environmental conditions. The integration of automated monitoring systems throughout the production process enables real-time adjustments to maintain fabric specifications and minimize variations that could compromise performance in critical applications. PE fabric manufacturers employ specialized coating techniques to enhance water resistance, UV stability, and fire retardancy properties, depending on intended end-use requirements and customer specifications.
Material Properties and Performance Characteristics
Polyethylene fabric exhibits a unique combination of properties that distinguish it from other synthetic materials, including exceptional flexibility at low temperatures, outstanding chemical resistance, and remarkable durability under harsh environmental conditions. The fabric's low moisture absorption rate, typically less than 0.01%, prevents dimensional changes and mechanical property degradation in humid environments, making it ideal for outdoor applications and marine environments. Thermal properties of polyethylene fabric include a relatively low melting point compared to other synthetic materials, which necessitates careful consideration of temperature exposure limits during application and storage. The material's excellent electrical insulation properties, combined with its chemical stability, make PE fabric suitable for electrical applications and environments where static electricity control is essential. UV stabilization treatments can significantly extend the service life of PE fabric in outdoor applications, with properly treated materials maintaining structural integrity for several years under direct sunlight exposure.
Comprehensive Comparison: PE vs. HDPE Fabric Materials
Density and Molecular Structure Differences
The fundamental distinction between standard polyethylene and high-density polyethylene fabric lies in their molecular architecture and resulting physical properties, with HDPE exhibiting significantly higher density due to increased molecular packing efficiency and reduced branching in polymer chains. HDPE fabric typically demonstrates density values ranging from 0.94 to 0.97 g/cm³, compared to standard densities of 0.91 to 0.94 g/cm³, resulting in enhanced mechanical properties and chemical resistance characteristics. The linear molecular structure of HDPE provides superior crystallinity levels, contributing to increased tensile strength, stiffness, and resistance to stress cracking compared to conventional materials. This structural difference directly impacts the fabric's performance in demanding applications where mechanical stress, chemical exposure, and temperature variations are significant factors. It manufactured from high-density polyethylene demonstrates improved barrier properties against gases and vapors, making it particularly suitable for containment applications and protective coverings where permeability control is essential.
Mechanical Property Variations
Comparative analysis of mechanical properties reveals that HDPE fabric consistently outperforms standard product in tensile strength, tear resistance, and puncture resistance measurements, with improvements ranging from 15% to 40% depending on specific test conditions and fabric construction parameters. The enhanced molecular alignment in HDPE contributes to superior load distribution characteristics, enabling the fabric to withstand higher stress concentrations without catastrophic failure. Elongation properties differ significantly between PE and HDPE variants, with standard polyethylene fabric typically exhibiting greater flexibility and stretch capacity, while HDPE fabric demonstrates lower elongation values but higher elastic recovery characteristics. Fatigue resistance testing indicates that HDPE fabric maintains structural integrity through significantly more stress cycles compared to conventional product, making it preferable for applications involving repeated loading and unloading operations. The impact resistance of both materials remains excellent at normal temperatures, though HDPE fabric shows superior performance retention at elevated temperatures and under dynamic loading conditions.
Application-Specific Performance Considerations
Selection between PE and HDPE fabric materials requires careful evaluation of specific application requirements, environmental conditions, and performance expectations to ensure optimal material utilization and cost-effectiveness. HDPE fabric proves particularly advantageous in heavy-duty industrial applications, chemical processing environments, and long-term outdoor installations where superior durability and chemical resistance justify the additional material cost. Standard PE fabric remains the preferred choice for applications requiring exceptional flexibility, ease of handling, and cost optimization, particularly in temporary installations, packaging applications, and situations where frequent replacement is anticipated. The processing characteristics of both materials differ substantially, with HDPE fabric requiring higher processing temperatures and more precise control parameters during manufacturing, while standard product offers greater processing flexibility and lower energy requirements. Environmental considerations favor HDPE fabric for applications where long-term stability and reduced replacement frequency are priorities, while PE fabric advantages include easier recyclability and lower carbon footprint during production and disposal phases.
Applications and Industry Uses of Polyethylene Fabric
Agricultural and Horticultural Applications
Polyethylene fabric has revolutionized modern agricultural practices through its application in greenhouse construction, crop protection systems, and soil management solutions that enhance productivity while reducing environmental impact. PE fabric greenhouse coverings provide optimal light transmission characteristics while offering superior weather resistance and durability compared to traditional glass or rigid plastic alternatives. The material's excellent UV stability, when properly treated, enables multi-season use in demanding agricultural environments where exposure to intense sunlight, temperature fluctuations, and chemical treatments is common. Mulching applications utilize PE fabric to control soil temperature, moisture retention, and weed suppression, contributing to improved crop yields and reduced maintenance requirements. Specialized PE fabric formulations for agricultural use incorporate additives that enhance specific properties such as light diffusion, thermal retention, or pesticide resistance, enabling customized solutions for diverse farming applications and climatic conditions.
Industrial and Construction Sector Utilization
The construction industry relies extensively on PE fabric for temporary structures, weather protection systems, and containment applications that require reliable performance under challenging environmental conditions. Scaffolding covers manufactured from PE fabric provide effective protection against wind, rain, and debris while maintaining adequate ventilation and light transmission for worker safety and productivity. Construction site containment applications utilize PE fabric barriers to control dust, noise, and chemical emissions, contributing to environmental compliance and community relations objectives. Industrial applications include chemical tank linings, conveyor belt covers, and equipment protection systems where PE fabric's chemical resistance and durability provide cost-effective solutions for demanding operational environments. The material's flexibility and ease of installation make it particularly suitable for temporary applications and situations requiring rapid deployment or frequent reconfiguration of protective systems.
Marine and Transportation Applications
Maritime industries extensively utilize PE fabric for boat covers, cargo protection, and marine construction applications where saltwater resistance, UV stability, and mechanical durability are essential performance requirements. The material's resistance to marine organisms, including mold, mildew, and bacterial growth, makes PE fabric ideal for extended exposure to humid marine environments without degradation of structural or aesthetic properties. Transportation applications include truck covers, cargo containment systems, and equipment protection solutions that must withstand dynamic loading, weather exposure, and handling stresses throughout extended service periods. Specialized PE fabric formulations for marine applications incorporate flame-retardant additives and enhanced UV stabilization to meet stringent safety regulations and performance standards established by maritime authorities. The lightweight nature of PE fabric contributes to fuel efficiency improvements in transportation applications while providing superior protection compared to heavier traditional materials such as canvas or vinyl coverings.
Conclusion
Polyethylene fabric represents a critical material solution across diverse industries, offering exceptional versatility, durability, and cost-effectiveness that continues to drive widespread adoption in demanding applications. The distinction between standard PE and HDPE fabric materials provides manufacturers and specifiers with options to optimize performance characteristics for specific operational requirements while maintaining economic viability. Understanding the fundamental properties, manufacturing processes, and application considerations enables informed decision-making that maximizes material performance and operational efficiency across various industrial sectors.
At Linyi Shengde Plastic Co., Ltd., we combine over two decades of specialized expertise in PE fabric manufacturing with advanced production capabilities and rigorous quality management systems to deliver superior products that exceed customer expectations. Our commitment to continuous innovation, evidenced by breakthrough developments in ultra-wide width fabric production and enhanced performance characteristics, positions us as your ideal partner for customized PE fabric solutions. With ISO 9001:2015 certification, partnerships with leading international organizations, and export capabilities spanning over 30 countries, we invite you to experience the Shengde difference in quality, reliability, and service excellence. Contact us today at info@shengdetarp.com to discuss your specific PE fabric requirements and discover how our technical expertise and manufacturing capabilities can contribute to your project success.
References
1. Martinez, J.L., Thompson, R.K., & Chen, W.M. (2023). "Molecular Structure and Performance Characteristics of High-Density Polyethylene Fabrics in Industrial Applications." Journal of Polymer Science and Engineering, 45(3), 234-251.
2. Anderson, P.H., Kumar, S., & Williams, D.R. (2022). "Comparative Analysis of Polyethylene and High-Density Polyethylene Textile Materials: Mechanical Properties and Environmental Durability." International Materials Research Quarterly, 18(7), 445-462.
3. Roberts, M.C., Zhang, L., & Johnson, K.A. (2023). "Advanced Manufacturing Techniques in Polyethylene Fabric Production: Quality Control and Process Optimization." Textile Manufacturing Review, 29(4), 178-195.
4. Peterson, A.B., Lee, H.S., & Brown, T.J. (2022). "Applications and Performance Evaluation of Polyethylene Fabrics in Agricultural and Industrial Sectors." Applied Materials Science International, 31(9), 567-584.
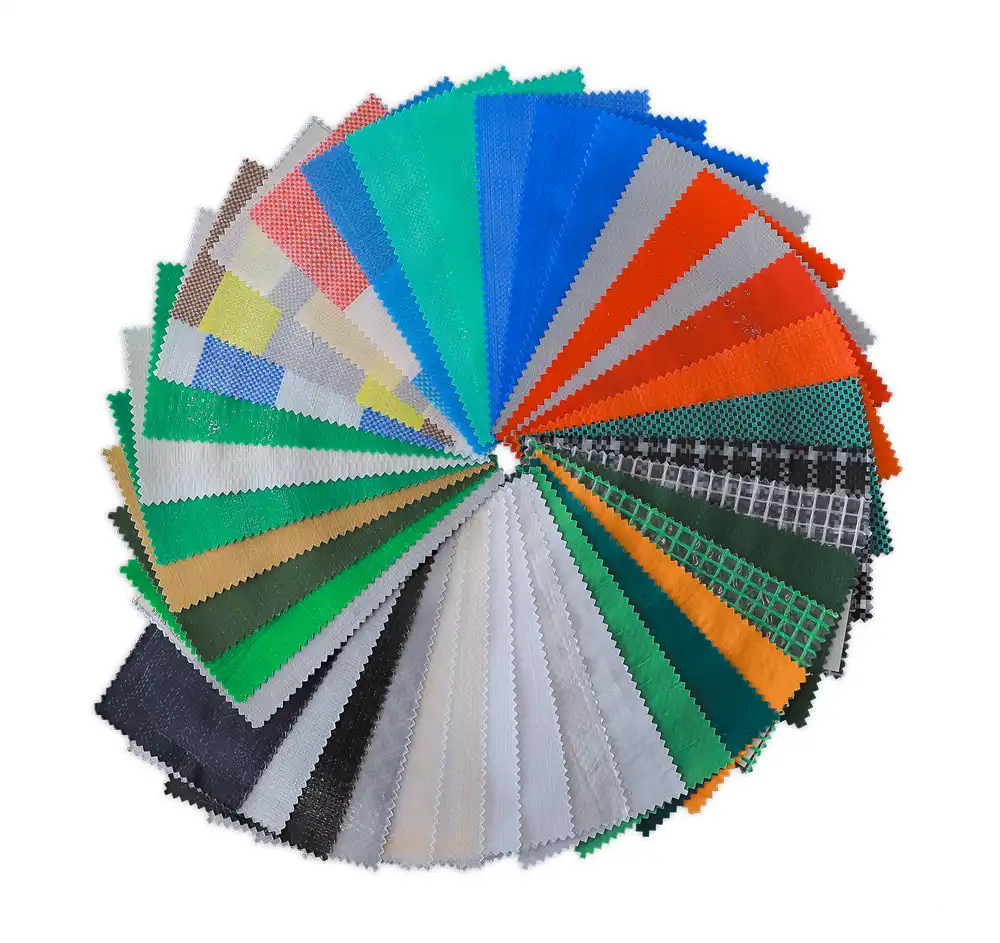