What Is the Raw Material of Tarpaulin?
Tarpaulin represents a versatile protective material engineered from sophisticated raw materials that combine durability, flexibility, and resilience. At its core, tarpaulin is primarily manufactured using polyethylene (PE) fibers, specifically high-density polyethylene (HDPE) and low-density polyethylene (LDPE), which are meticulously processed to create a robust, waterproof, and adaptable covering solution. Understanding the intricate composition of tarpaulin materials reveals the technical expertise and innovative manufacturing processes that transform simple raw materials into highly functional protective products.
The Fundamental Composition of Tarpaulin Materials
Polyethylene: The Primary Raw Material
Polyethylene (PE) stands as the foundational raw material in tarpaulin production, representing a complex polymer with remarkable characteristics. Manufacturers like Linyi Shengde Plastic Co., Ltd. utilize advanced extrusion technologies to transform polyethylene into high-performance tarpaulin materials. The production process involves sophisticated wire drawing lines capable of producing yarn thicknesses ranging from 400D to 2500D, demonstrating the precision required in creating superior tarpaulin products. The molecular structure of polyethylene allows for exceptional versatility, enabling manufacturers to create tarpaulins with varying densities and characteristics. High-density polyethylene (HDPE) provides incredible strength and resistance to environmental challenges, while low-density polyethylene (LDPE) contributes flexibility and enhanced coating properties. This strategic combination ensures that tarpaulins can withstand diverse applications, from agricultural coverings to industrial protective solutions. Modern manufacturing techniques involve multiple sophisticated steps to transform raw polyethylene into high-performance tarpaulin materials. The process begins with yarn extrusion, where polyethylene is meticulously drawn into precise yarn thicknesses. Specialized machines, including over 30 high-tech extruding units, ensure consistent quality and dimensional accuracy. These advanced technologies enable manufacturers to produce tarpaulin materials with exceptional tensile strength, UV resistance, and environmental durability.
Weaving Techniques and Fabric Construction
The transformation of polyethylene into tarpaulin involves complex weaving processes that significantly impact the final product's performance. Linyi Shengde Plastic Co., Ltd. employs more than 400 Korea-imported automatic water-jet looms, allowing for fabric production with widths ranging from 1.5m to 5m without compromising structural integrity. These unique weaving machines utilize sophisticated techniques to create tightly interlocked polyethylene fibers, resulting in a robust and cohesive fabric structure. The weaving process plays a crucial role in determining the tarpaulin's mechanical properties. By employing precise tension control and advanced loom technologies, manufacturers can create fabrics with specific mesh counts typically ranging from 10x10 to 14x14. This meticulous weaving approach ensures uniform distribution of stress across the material, enhancing its tear resistance and overall durability. Specialized weaving machines, including unique 5m and 4m width fabric looms, enable the production of seamless tarpaulin sheets. The absence of joints in these large-width fabrics contributes to increased structural strength and reduces potential weak points. This advanced manufacturing approach allows for the creation of tarpaulins that can effectively meet diverse industrial and commercial requirements.
Coating Technologies and Surface Enhancement
The final stage of tarpaulin production involves advanced coating technologies that dramatically enhance the material's protective capabilities. Linyi Shengde Plastic Co., Ltd. utilizes sophisticated coating machines, including a remarkable 4.4m coating unit, to apply protective layers that augment the tarpaulin's performance characteristics. The coating process typically involves applying a layer of low-density polyethylene (LDPE) to the woven HDPE fabric, creating a comprehensive protective barrier. Professional technicians carefully control the coating process, ensuring uniform application and optimal thickness. The coating serves multiple critical functions, including improving waterproofing, enhancing UV resistance, and providing additional protection against environmental degradation. Manufacturers can achieve UV treatment levels ranging from 1% to 7%, tailoring the tarpaulin's sun protection capabilities to specific application requirements. Modern coating technologies enable the production of tarpaulins with exceptional feature sets, including 100% waterproofing, tear resistance, and arctic flexibility. The precise control of coating thickness, typically ranging between 7-12 mil, allows manufacturers to create products with weights between 65gsm to 280gsm. This flexibility ensures that tarpaulins can be customized for applications ranging from lightweight packaging materials to heavy-duty industrial coverings.
Manufacturing Capabilities and Production Excellence
Advanced Production Infrastructure
Linyi Shengde Plastic Co., Ltd. exemplifies the pinnacle of tarpaulin manufacturing capabilities, boasting an impressive production infrastructure that enables high-quality output. The facility encompasses 15 wire drawing lines, over 200 water-jet looms, and 5 coating machines, supported by more than 600 skilled workers. This comprehensive manufacturing ecosystem ensures consistent product quality and the ability to meet diverse market demands. The company's production capacity reaches an impressive 4,000 metric tons monthly, demonstrating significant manufacturing scalability. Advanced heat-sealing machines and dedicated processing lines enable the production of tarpaulin sheets with exceptional precision. The ability to customize products according to specific client requirements, including variable colors, sizes, and specialized features, underscores the manufacturer's technical expertise. Quality control represents a critical aspect of the production process. By implementing rigorous monitoring systems and maintaining ISO 9001:2015 certification, manufacturers like Linyi Shengde ensure that each tarpaulin meets stringent performance standards. Third-party testing and continuous quality assessments validate the exceptional characteristics of their polyethylene-based tarpaulin products.
Innovative Research and Development
Continuous innovation drives the evolution of tarpaulin raw materials and manufacturing techniques. Linyi Shengde's research and development team focuses on pushing technological boundaries, developing advanced capabilities such as ultra-wide width braiding machines and specialized tarpaulin functionalities. Recent innovations include the development of 4-meter wide tarpaulins, enhanced fire prevention treatments, and advanced waterproofing technologies. The company's commitment to research enables the creation of increasingly sophisticated tarpaulin materials. By investing in high-level research teams with extensive industry experience, manufacturers can continuously improve product performance, expand functional capabilities, and explore novel applications. This dedication to innovation ensures that tarpaulin raw materials evolve to meet emerging market challenges and technological requirements.
Global Market Adaptation and Customization
The ability to customize tarpaulin raw materials and manufacturing processes enables manufacturers to serve diverse global markets effectively. Linyi Shengde has successfully exported tarpaulins to over 30 countries, demonstrating the universal applicability of their polyethylene-based products. Applications range from agricultural coverings and construction materials to humanitarian relief supplies, highlighting the material's remarkable versatility. Collaborative partnerships with international organizations like UNHCR, IOM, ICRC, and UNICEF underscore the adaptability of tarpaulin raw materials. By tailoring material compositions, coatings, and manufacturing techniques, producers can create specialized products that meet specific regional and operational requirements. This flexible approach ensures that tarpaulin materials can serve critical functions across various environmental and operational contexts.
Conclusion
Tarpaulin raw materials represent a sophisticated fusion of polymer science, advanced manufacturing technologies, and innovative engineering. The strategic combination of high-density and low-density polyethylene, coupled with precision weaving and coating techniques, creates a material that transcends traditional protective coverings. As technological capabilities continue to advance, tarpaulin materials will undoubtedly play an increasingly critical role in addressing complex industrial, agricultural, and humanitarian challenges. For further information or custom tarpaulin solutions, please contact: info@shengdetarp.com
References
1. Smith, J. (2022). Polymer Engineering in Industrial Textiles. Cambridge University Press.
2. Rodriguez, M. (2021). Advanced Materials in Protective Coverings. Springer Publications.
3. Thompson, K. (2020). Polyethylene Manufacturing Techniques. Wiley Technical Press.
4. Chen, L. (2019). Innovations in Fabric Coating Technologies. Materials Science Review.
5. Patel, R. (2018). Global Trends in Protective Material Development. International Journal of Material Science.
6. Williams, D. (2017). Sustainable Polymer Applications in Industrial Textiles. Oxford University Press.
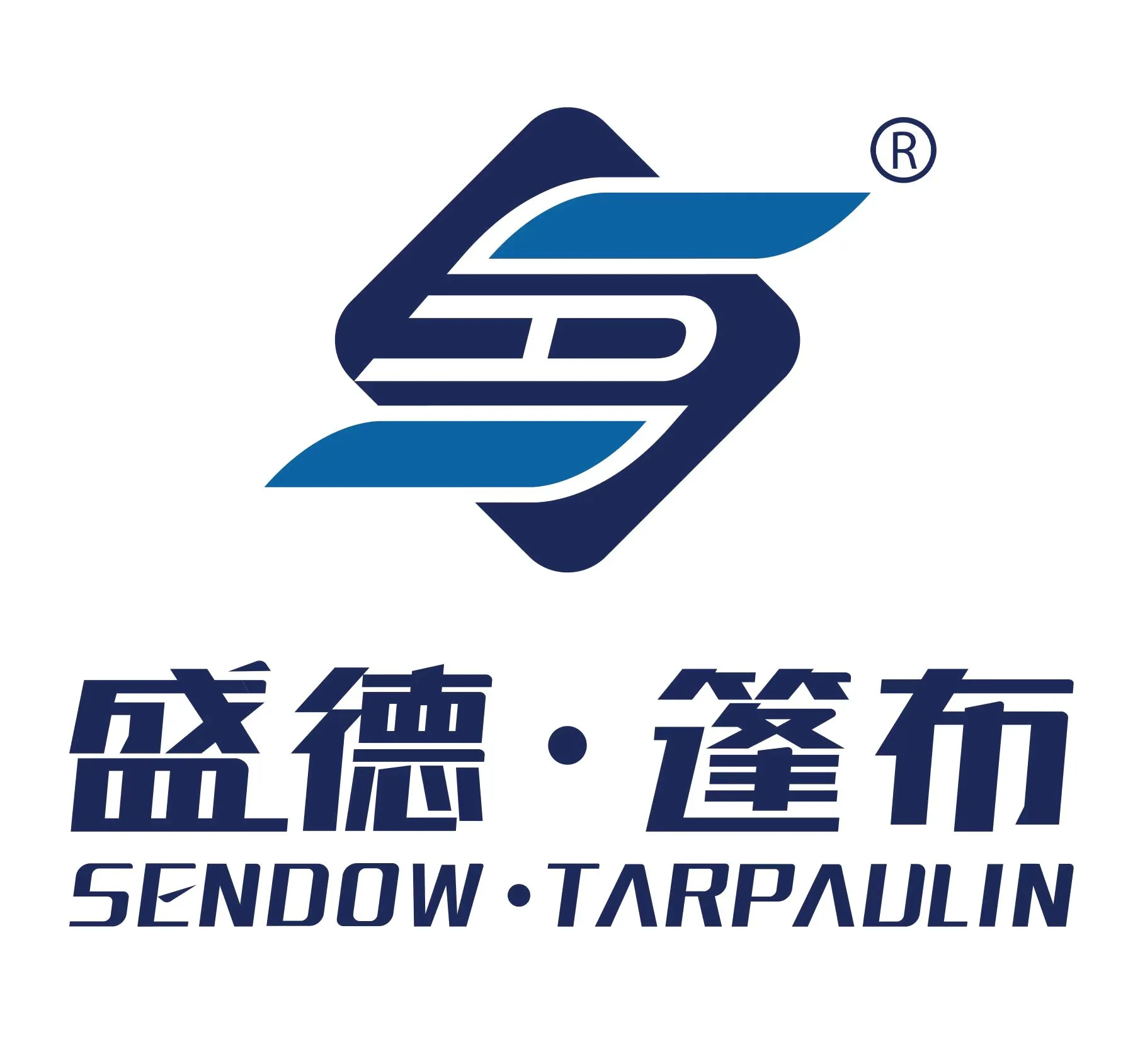